Why Manufacturers and OEMs with Track and Trace Systems Thrive
In recent years, industrial track and trace systems have shifted from a “nice-to-have”x9d element for manufacturing operations to an essential component in remaining competitive. The question is no longer if a manufacturer should implement traceability infrastructure, but when. Companies with systems already in place are reaping the benefits of greater efficiency, profitability, and a leading edge.
But, first, what exactly is traceability?
Streamlining Operations & Boosting the Bottom Line with Traceability
In a commercial context, the term refers to tracking a product through every phase of its lifecycle. For original equipment manufacturers (OEMs), their suppliers, and their sub-suppliers, traceability produces a trackable trail for each material, component, and final product across all operations and processes.
Savvy manufacturers are developing their traceability infrastructure to connect with the Internet of Things (IoT), the system of devices, machines, and objects tagged with unique identifiers (UIDs)—including barcodes—to transfer data over a network. Connected track and trace solutions allow companies to view data in real-time, gain the insight needed to streamline operations and, ultimately, boost the bottom line.
Traceability infrastructure also plays a critical role in managing a challenge faced by virtually every manufacturer: product recalls. Parts and components with traceability markings create a documented history spanning every step of the manufacturing process. If a product containing one of these parts is recalled, manufacturers can easily provide evidence of compliance with safety and quality standards.
Automotive manufacturers and suppliers have demonstrated that traceability systems can effectively contain recalls that are far wider-reaching and have drivers’ lives on the line. Takata, an auto supplier, was forced to recall nearly 67 million airbags after a spate of deadly accidents. The firm’s airbags were found to be prone to rupturing or exploding upon inflation, or the airbags’ inflator components could spray shrapnel during an accident. During the first four years of the recall campaign, 70% of airbags were replaced per the National Highway Traffic Safety Administration. The rest are still being tracked and traced through DMVs, used car lots, service centers, auction centers, and other resources. No doubt, barcodes on subassemblies and other production data tied to a car’s vehicle identification number (VIN) play a role in tracking down the remaining airbags.
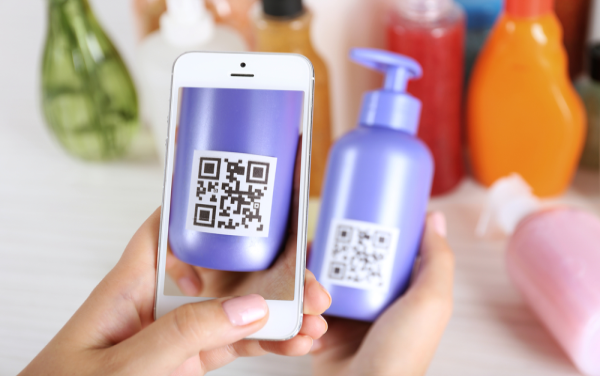
Barcodes enhance traceability in the event of a recall—from ingredients to end product.
A Fruitful Track & Trace Framework for the Wine Industry
Traceability is crucial in industrial or automotive manufacturing, but its applications extend well beyond these industries. From traceable “plant passports”x9d that reduce the spread of pests across the EU to the track and trace systems cracking down on illicit cigarette trade in Russia, use cases for traceability solutions are vast and diverse.
For the wine industry, implementing a traceability framework proved beneficial for consumers and purveyors alike. Historically, the supply chain for commercial winemaking has been complex and fragmented, with many parties and stakeholders involved. However, as wine consumers expressed increasing interest in the provenance of each bottle for purchase, demand for an industry-wide track and trace protocol intensified.
Forming a working group to tackle the challenge, nonprofit standards organization GS1 and its collaborators identified the key players in commercial winemaking: grape growers, wine producers, bulk distributors, transit cellars, fillers/packers, distributors, and retail stores. Establishing clear labeling standards for each stakeholder in the process, the group developed a comprehensive framework for capturing and transmitting pertinent data across the entire supply chain.
Now, when GS1-compliant growers send products to producers, they label shipments with Global Location Numbers (GLNs). In addition to identifying the vineyard and exact plot the grapes were grown in, these GLNs include information about the number and variety of vines the plot contains.
The GS1 traceability framework employs many coding formats like GS1-128 barcodes, Universal Product Codes (UPCs), and European Article Numbers (EANs). These ensure that this data and other necessary information travels through each part of the supply chain intact. And in the final link in the chain, when a discerning consumer asks questions about the provenance of a bottle of wine, sellers have immediate access to information in a scannable format.
Traceability is in Your Reach
The idea of implementing traceability infrastructure may sound daunting, but it doesn’t have to be. Your organization can start small by considering the points below and expand its track and trace capabilities as needed.
- Think about the big picture
Ideally, your organization will put a system in place that meets your needs today and will grow as your business does. Important considerations include your company’s long-term goals or objectives, trends impacting the way your product will be made in the future, regulations you need to comply with, and projections about shifting customer wants and needs. - Determine what data you need to track and trace
With short- and long-term objectives for your traceability infrastructure established, consider the identifying information required to track and trace your parts, materials, or products. For manufacturers and OEMs, this data can include a model number, batch number, manufacturing date, and UID for each unit.
- Make your mark
By now, it’s easy to assume that barcodes are practically everywhere. And because that assumption is spot on, the actual barcode and ID labels themselves, such as those from Brady Corporation, have evolved. Need to track assets, such as hand tools or carts, in a food production facility that’s subject to harsh cleaners and near-constant water? Washdown-resistant labels are available, as are smudge-resistant and high-temperature labels—just to name a few.Of course, not all materials, e.g., metal, are conducive to labels. Among the most popular solutions is direct part marking (DPM) that typically uses a laser or acid to engrave pertinent product or production data. And because recalls can involve the smallest automotive or medical device components, Rel8, a Danish traceability expert, created imZERT® technology. The firm recently pioneered a method of using nanostructures to engrave plastics and elastomers with some of the world’s smallest barcodes. There’s always a way to mark the components or finished products your business provides—even if it’s just through packaging. - Choose a coding system that meets your needs
Once you’re clear on your organization’s objectives and you know what data you’ll be tracking and tracing, you can consider the kind of infrastructure you’ll implement. Do your products require an image-based scanning solution? A software-based barcode scanning system? A hardware-based barcode scanning platform?
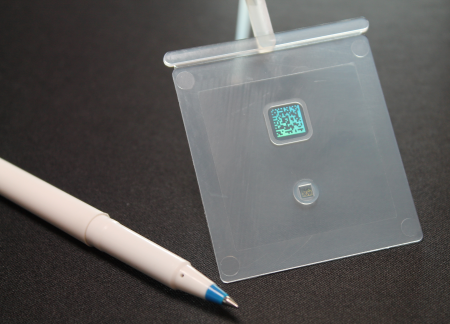
imZERT barcode tech marks small parts for track & trace.
- Contact Code Corp
Integrating track and trace is easier than most might expect. And industrial track and trace experts and barcode manufacturers can help—after all, their products are the ones bearing the barcodes. For guidance in getting started and/or capturing data within your track and trace system, contact Code Corporation. We can help you find the right barcode readers or barcode scanning software to support your organization’s traceability infrastructure.
Share This Post
Author
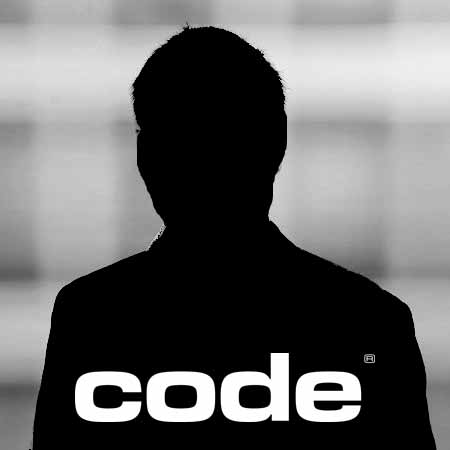
Paul Garcia
Many of the talented and qualified staff at Code Corporation contribute to our blog. Our team members add a unique perspective to our communications efforts, and we are fortunate to have such a great cadre of writers as part of our company.