Aerospace is experiencing turbulence. In 2019, robust travel and space exploration propelled the sector; Covid 19 grounded everything. In 2023, “revenge travel” and lifted restrictions roiled commercial aviation and strained suppliers. Moreover, inflation and mercurial oil prices have dampened any rebound.
To cope, aerospace manufacturers are embracing resilience-boosting tech, like the reyda asset tracking app. Brainchild of Berlin-based MGBM-Development GmbH, reyda is one of aviation’s most comprehensive asset management platforms.
“reyda is aerospace’s go-to for real-time track and trace within manufacturing jet engines and aeronautical components,” shares Mark Gennotte, MGBM’s CEO. “However, as an intuitive hybrid app, reyda reigns over all traceability solutions because it can shape sustainability, tighten quality, and support regulatory compliance.”
A cloud-based platform that collects data via smartphone, reyda syncs with a small or midsize firm’s enterprise management systems, funneling KPIs from a process or asset into dynamic dashboards. Customizable and compatible with all smart devices and PCs, reyda gives personnel up-to-the-minute data to facilitate revenue-driving decisions.
“Sales and quality management, for instance, can outpace production bottlenecks with reyda,” he shares. “Production workers can locate specific tools via reyda-equipped devices and then watch a video on their device about using that tool for a particular process—reyda’s really that powerful.”
How does reyda do it all? Barcodes.
Built Right for Flight with Barcodes
Granular traceability is crucial for jet engines with 25,000-50,000 parts. While scanning electronics’ DPM barcodes in a clean room is one thing, scanning dot peen codes on metal becomes challenging—especially from scaffolding in a runway-equipped factory.
“Understandably, these conditions are taxing because human safety relies on quality,” Gennotte says as he reflects on his aviation career. “Further complicating things is that aerospace suppliers and OEMs seek high-caliber employees in a shallow labor pool.”
These cascading difficulties gave reyda a chance to do—and mean—more for aviation. However, accomplishing this hinged on the right barcode scanning solution.
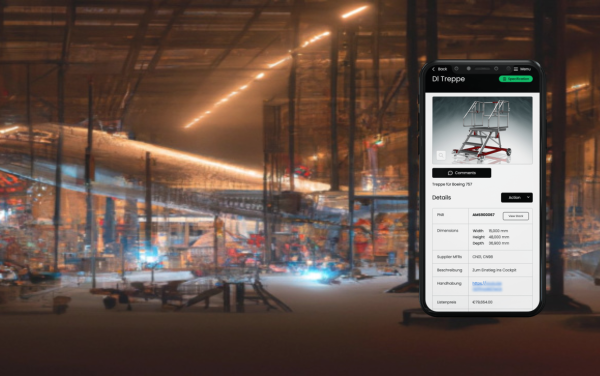
reyda asset tracking app traces components during assembly with Code’s CortexDecoder SDK.
Barcode Scanning SDKs Take Off
MGBM zeroed in on barcode scanning software development kits (SDKs) to support reyda. The ideal SDK should read all barcode types in any condition while being cloud-friendly to fuel reyda’s extensive real-time intelligence capabilities.
“We tested every barcode scanner OEM’s scanning library with Microsoft, Android, and iOS devices,” Gennotte reveals. “reyda’s point-and-shoot operation is inherently clear, so the SDK had to be easy to use.”
Back-to-back testing within lab and factory settings led MGBM’s developers to select Code Corporation’s barcode scanning CortexDecoder SDK, thanks to its speed and decoding capability.
“Especially when scanning data matrix labels that are vibro peened, etched, or lasered on a component,” Gennotte notes. “In addition, Code’s algorithm reads labels that are damaged or those in suboptimal lighting, giving us a potent mobile scanning solution.”
Enabling reyda to scan any barcode symbology on shiny, matte, or scuffed materials, he adds, gives rise to digital twins.
“The result is a state-of-the-art, cloud-based technology that can be deployed at any stage in a product’s lifecycle,” Gennotte adds. “Without Code’s scanning algorithm, we can’t fully demo the true concept of a ‘digital twin.’”
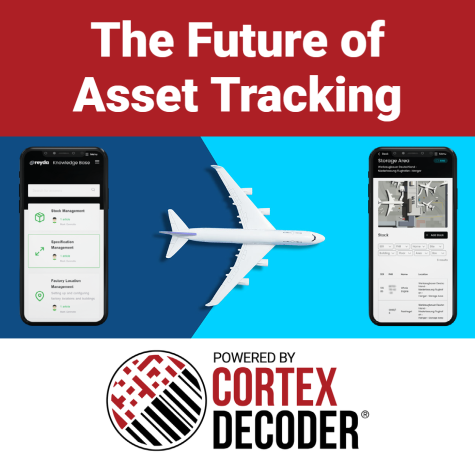
Code’s CortexDecoder enables reyda to capture KPIs and transmit them to dashboards.
Preparing reyda for Takeoff
Buoyed by aerospace success, MGBM is confident that reyda’s inherent strengths will translate well to any small to medium enterprise (SME). Most SMEs rely on field services or assembly workers, need KPIs to empower operations, or would benefit from tightened traceability. In fact, MGBM is in talks with MH-Invelopment, one of Germany’s top digitalization experts, to guide reyda from runways to office parks. As such, they’re demonstrating reyda on Gigaset’s made-in-Germany B2B smartphones.
“Running reyda on Gigaset phones demonstrates cost-savings,” Gennotte explains. “We’re showing firms how to streamline device count while getting the same high-performance barcode scanning via CortexDecoder.”
Moreover, he adds, reyda’s capabilities perfectly showcase Gigaset’s performance.
“Working within a conglomeration where each entity brings the best ingredients to the table creates a recipe for success,” Gennotte muses.
reyda’s forecast calls for blue skies. The app’s success in aerospace has fortified safety for pilots, flight crew, passengers, and ground crew servicing systems between flights. Imagine the capabilities reyda holds for any SME seeking a competitive edge.
Unlocking a wealth of data with high-performance barcode scanning starts by contacting Code.
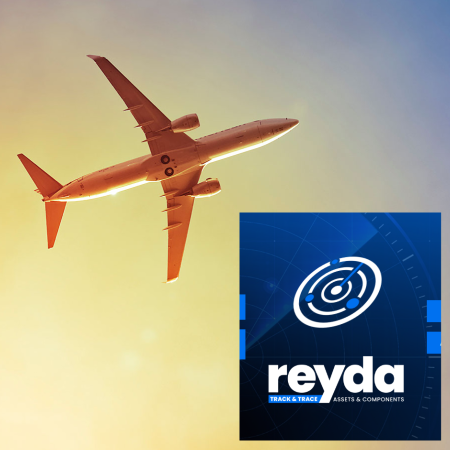
Share This Post
Author
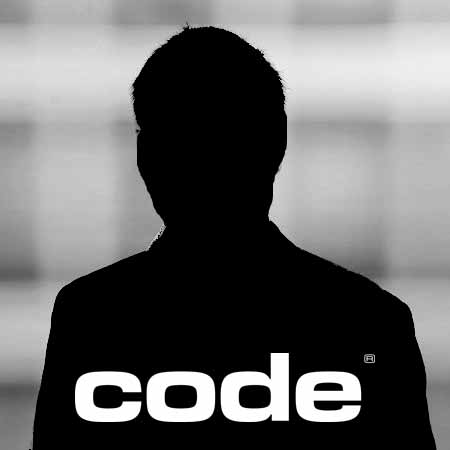
Paul Garcia
Many of the talented and qualified staff at Code Corporation contribute to our blog. Our team members add a unique perspective to our communications efforts, and we are fortunate to have such a great cadre of writers as part of our company.