Being direct: DPMs and their barcode readers are everywhere, here’s why
It’s time to direct your attention to direct part marking (DPM). Chances are high that you encounter DPMs several times a day: DPMs are barcodes used on the components in your phone. DPMs are scattered throughout the last car you rode in, and DPMs are even used to track the ingredients used in your medicine and cosmetics. Because they’re so important, we’re looking into the hows, whats and whys of DPM barcode technology.
Why was DPM developed?
Complex technology and machinery can include thousands of parts in their manufacture. The process of stamping a company name and sometimes model number and/or date on a piece of machinery or metal product goes back hundreds of years. But automation and robotics have taken over manufacturing and production assembly lines, moving direct human intervention further and further away from the manufacture of parts and equipment.
As this transition took place, businesses needed a way to track each individual part through the entire life cycle of the product, from parts production, to manufacture and assembly, throughout the supply chain, and even after deployment to whatever consumer (commercial, governmental, individual) for whom the product is intended. Direct part marking is the result of this need.
What is DPM?
Direct part marking is the process of permanently marking a part or piece in the manufacture of complex technological or mechanical machinery with a unique machine-readable code to track it throughout the product life cycle.
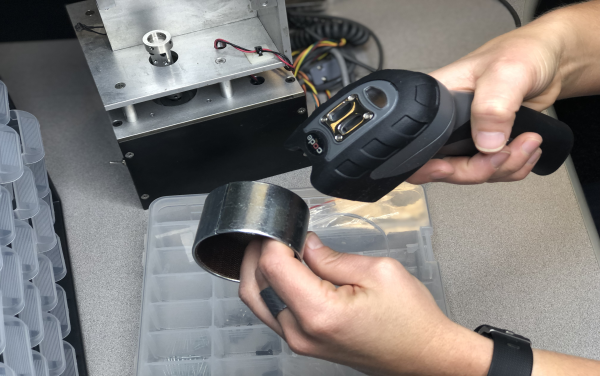
Select barcode readers can scan direct part marking on metal, glass, and plastic.
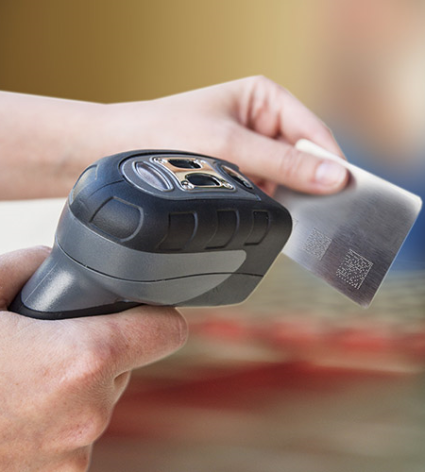
Example of DPM on brushed metal
Who uses DPM?
As mentioned earlier, the automotive industry was the first to make use of the QR code for direct part marking. The same is also true for data matrix codes, which were introduced by International Data Matrix, Inc. in 1994 to serve auto manufacturers. Direct part marking is also prevalent in the aerospace industry, where NASA has established a standard for direct part marking. DPM makes a lot of sense for electronics because the codes can be extremely small and still be readable by scanner technology. Process industries, such as pharmaceuticals, medical device manufacturers, and food and beverage are also gravitating to DPM to support product recalls and prevent counterfeit items from infiltrating their supply chains.
What are the benefits of DPM?
One of the main benefits of DPM barcodes is that, unlike most other barcode technologies, they are imprinted permanently onto the parts they identify. This improves the reliability of the codes, as they can withstand conditions that other common barcode technologies may not. A perfect example: the chassis components in a hard-working truck—over time, these components will be subjected to grime, water, grease, and mechanical forces that render other barcode type useless.
As mentioned above, DPM’s compact footprint makes it incredibly beneficial for use on packaging or in component-heavy products—particularly within the electronics, pharmaceutical, and medical device manufacturing industries. Best of all, manufacturers don’t need special equipment to decode DPMs—the right barcode reader can do the trick. And so can standard smartphones—a Danish company makes DPMs that are as small as 1mm2. Hailed as the “world’s smallest barcodes” for injection molding, these diminutive DPMs and be scanned by a smartphone equipped with a barcode scanning software development kit (SDK).
The machine-readability of these methods decreases the need for manual code entry, improves accuracy, reduces the likelihood of human error, and makes data exchange much faster and simpler.
If your business needs to scan parts for tracking or identification purposes, consider an industrially focused barcode scanner, such as Code Corp’s CR6000. The CR6000 was engineered to scan barcodes of every sort—on virtually any material such as metal, elastomer, or glass. The CR6000 effortlessly reads laser-etched, embossed, dot peen, postal, low-contrast, dense, or tiny barcodes (down to 2 mils).
If you are new to DPM barcodes and would like some guidance in selecting the right barcode scanning solution, contact us at info@codecorp.com or +01 801-495-2200.
Share This Post
Author
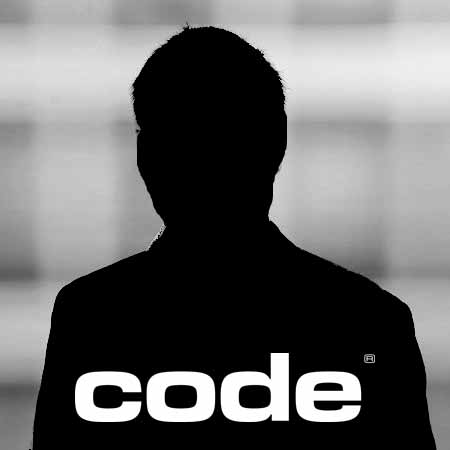
Paul Garcia
Many of the talented and qualified staff at Code Corporation contribute to our blog. Our team members add a unique perspective to our communications efforts, and we are fortunate to have such a great cadre of writers as part of our company.